Advanced Techniques in Modern Tank Welding Inspection
Advanced Techniques in Modern Tank Welding Inspection
Blog Article
The Necessary Duty of Storage Tank Welding Assessment in Ensuring Structural Stability and Security Compliance in Industrial Applications
In the realm of commercial applications, tank welding assessment emerges as an essential element in securing architectural integrity and making certain compliance with security regulations. Utilizing a mix of methods such as visual evaluations and progressed testing techniques, these inspections serve to recognize and mitigate prospective imperfections before they intensify right into substantial hazards.
Value of Container Welding Inspection

Making sure conformity with sector standards and regulations is an additional considerable element of storage tank welding assessment. Governing bodies mandate rigorous standards for the building and construction and upkeep of tank, and thorough inspections help organizations comply with these requirements. Non-compliance can result in severe penalties, including penalties and closures, better stressing the demand for strenuous examination procedures.
In addition, storage tank welding evaluation plays a crucial duty in preserving operational performance. In summary, the relevance of storage tank welding evaluation exists in its capability to safeguard public health and wellness, safeguard the setting, and guarantee conformity with regulative frameworks.
Secret Inspection Strategies
Reliable tank welding assessment relies upon a variety of crucial strategies that make certain complete assessment of weld high quality and architectural integrity. Among one of the most widespread techniques are visual examination, ultrasonic testing, radiographic screening, and magnetic fragment testing - Tank Welding Inspection. Each method uses one-of-a-kind advantages in evaluating various facets of the weld
Visual evaluation offers as the initial line of protection, allowing inspectors to determine surface area issues, abnormalities, or inconsistencies in the weld bead. Ultrasonic testing utilizes high-frequency acoustic waves to detect internal defects, such as cracks or gaps, providing a comprehensive assessment of weld stability. This technique is especially reliable in identifying issues that may not show up on the surface.
Radiographic testing utilizes X-rays or gamma rays to produce pictures of the welds, exposing inner discontinuities and providing a permanent record for future reference. This technique is highly effective for critical applications where the risk of failure must be minimized.
Last but not least, magnetic fragment screening is used to determine surface and near-surface problems in ferromagnetic materials. By applying electromagnetic fields and great iron fragments, examiners can identify suspensions that might compromise the architectural honesty of the storage tank. Together, these techniques form a durable structure for guaranteeing top quality welds in industrial applications.
Compliance With Security Specifications
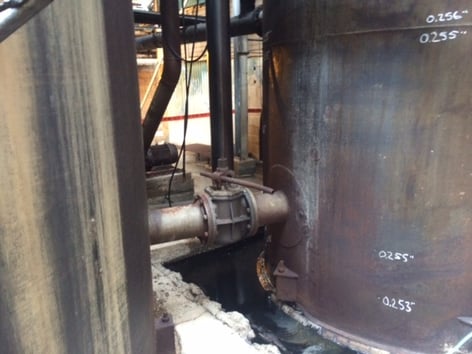
Routine inspections play a crucial function in ensuring conformity by identifying possible failures or inconsistencies from recommended standards. Examiners are trained to examine weld quality, click resources validate material requirements, and evaluate the total structural stability of storage tanks. Their experience is vital in making certain that welding processes fulfill the required safety and security standards.
In addition, conformity with safety requirements not just safeguards employees but likewise safeguards the setting from potential dangers such as leakages or devastating failings. Organizations that focus on safety conformity are much better positioned to reduce threats, enhance operational effectiveness, and cultivate a culture of security within their labor force. In recap, maintaining extensive compliance with safety standards is indispensable for the effective procedure of tank welding activities in industrial setups.
Advantages of Normal Evaluations
Routine assessments are indispensable to maintaining the architectural stability and safety of bonded containers. These assessments offer a systematic approach to identifying prospective flaws or weak points in the welds, making certain that any kind of concerns are addressed before they escalate right into substantial failings. By conducting regular analyses, organizations can detect rust, exhaustion, and other forms of deterioration that may jeopardize storage tank performance.
In addition, constant examinations contribute to conformity with sector laws and criteria. Sticking to these guidelines not only reduces legal threats yet additionally improves the organization's credibility for security and reliability. Regular examinations cultivate a positive security culture, encouraging staff members to identify and prioritize the significance of equipment honesty.
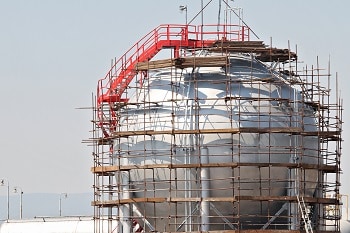
Case Researches and Real-World Applications
Situation studies and real-world applications highlight the concrete impact of reliable storage tank welding inspection techniques. One significant example is a huge petrochemical facility that encountered considerable operational disruptions as a result of leakages in tank. Complying with the execution of extensive welding you can try these out inspection procedures, including aesthetic and ultrasonic testing, the facility recognized essential defects in weld seams that could have resulted in catastrophic failings. This proactive technique not only stopped ecological hazards yet also saved the firm millions in potential cleaning costs and regulative penalties.
Similarly, a water treatment plant applied a comprehensive evaluation program for its storage tank welding procedures - Tank Welding Inspection. By including non-destructive testing methods, the plant was able to find very early signs of corrosion and fatigue in weld joints. This prompt intervention extended the life expectancy of the storage tanks and made certain compliance with security regulations, thus protecting public health and wellness
These situation researches emphasize the relevance of normal and systematic tank welding inspections. By prioritizing these practices, industries can mitigate risks, enhance structural integrity, and make certain conformity with safety requirements, inevitably leading to improved operational performance and lowered responsibilities.

Conclusion
In conclusion, container welding examination is a crucial part of preserving structural integrity and safety and security in commercial applications. Utilizing various inspection strategies makes sure early detection of possible problems, thus avoiding catastrophic failings. Adherence to safety standards further boosts operational reliability and conformity with regulative needs. Eventually, regular examinations not only protect public straight from the source wellness and the atmosphere but likewise contribute to the long life and efficiency of essential possessions, underscoring the crucial role of this technique in industrial procedures.
Report this page